رزین های آلکیدی به عنوان ماده اولیه برای تولید رنگ ها و لاک های مدرن یکی از جایگاه های پیشرو را به خود اختصاص داده اند. ترکیبات تشکیل دهنده فیلم بر اساس آنها کاربردهای گسترده ای دارند. خواص پوشش بستگی به نوع رزین ها و لاک های نیمه تمام دارد. رایج ترین آنها ترکیبات اصلاح شده هستند، زیرا دارای ویژگی های تزئینی و محافظتی بالایی هستند.
شرح
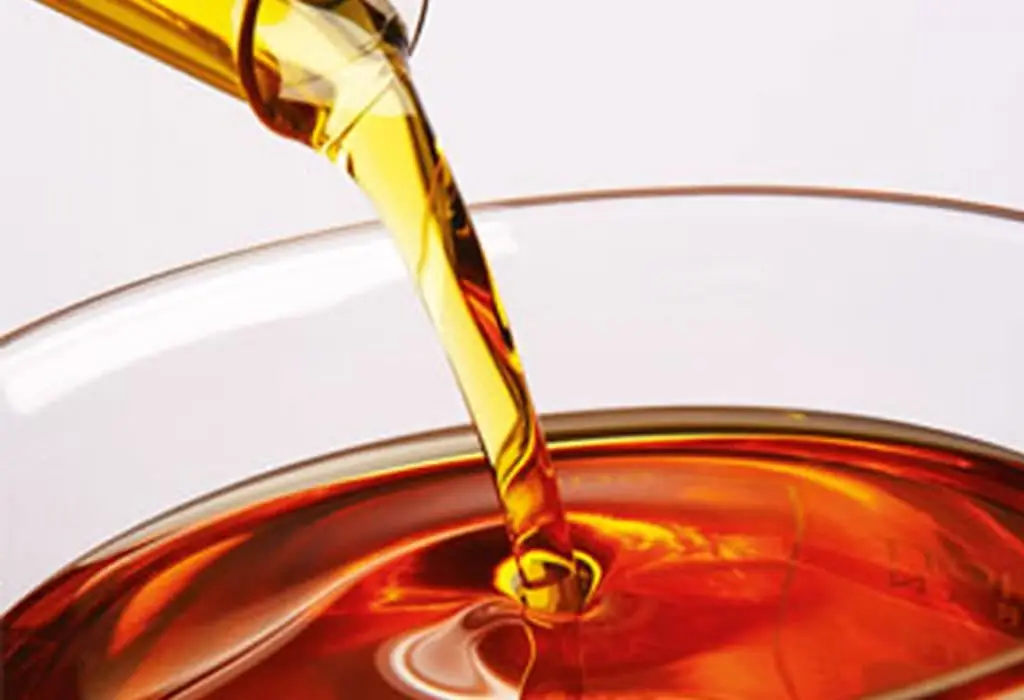
رزینهای آلکیدی (یا آلکیدها) استرهایی هستند که از واکنش الکلهای پلیهیدریک با اسیدهای پلیبازیک یا انیدریدهای آنها به دست میآیند. از نظر ظاهری توده ای چسبناک بسیار چسبناک هستند که رنگ آن از زرد تیره تا قهوه ای است.
آلکیدها همچنین با رزین های دیگر و سلولز (آلکید-اوره- فرمالدئید، فنل-آلکید، کوپلیمرهای آلکید-اکریلیک و سایر ترکیبات) ترکیب می شوند. برای کاهش کشش سطحی، بوتیل الکل به ترکیب آنها اضافه می شود که ریختن محصول نهایی را آسان تر می کند.
ترکیب شیمیایی و طبقه بندی
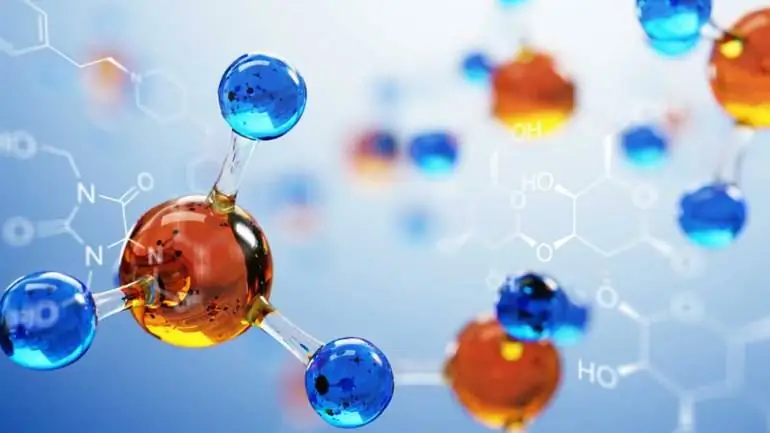
رزین های آلکیدی بر اساس چندین معیار سیستماتیک می شوند:
- با وجود اسیدهای چرب در ترکیب: اصلاح نشده (فتالات) و اصلاح شده.
-
بر اساس محتوای روغن: چرب (>60%)، چربی متوسط (40-60%)، بدون چربی (35-60%)، فوق لاغر (<34%). آلکیدهای چرب عمدتاً با روغن های خشک کننده تهیه می شوند.
- با توجه به نوع الکلی که بر اساس آن ترکیب به دست می آید: گلیفتالیک، گزیفتالیک، پنتافتالیک، تریفتالیک.
- با قابلیت خشک کردن: خشک کردن و غیر خشک کردن.
- طبق روش انحلال: رقیق شده با حلال های آلی یا آب.
ترکیب شیمیایی رزین آلکیدی محلول ۴۰ تا ۶۰ درصدی مواد غیرفرار در حلالهای آلی است.
ویژگی ها
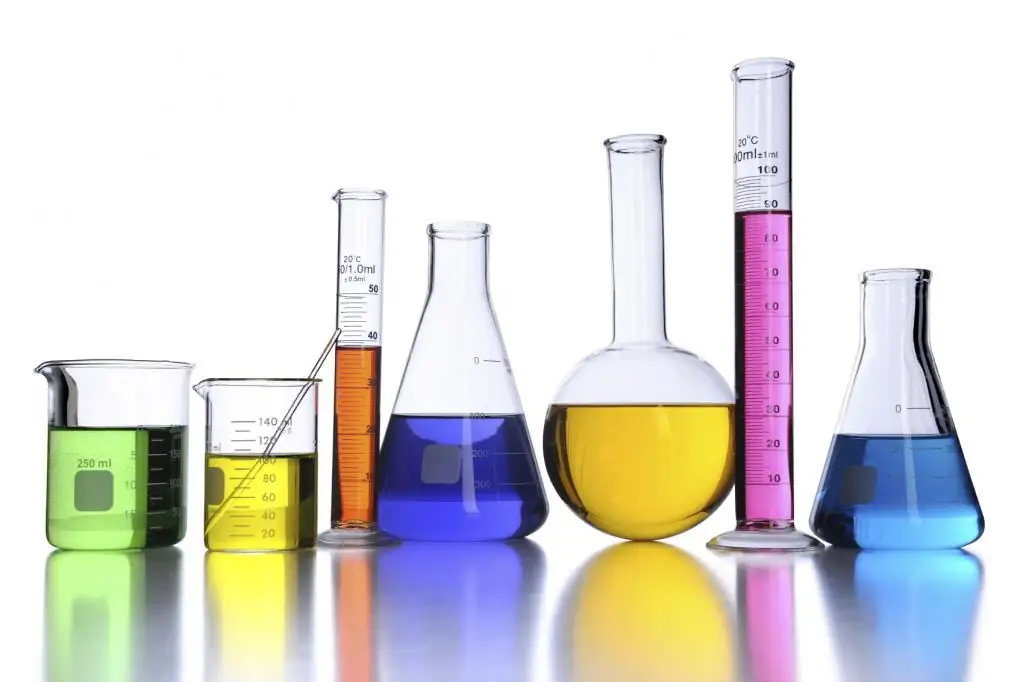
خواص آلکیدها به نوع الکل پلی هیدریک، غلظت آن و وجود اجزای دیگر بستگی دارد. اجزای معطر بر اساس این ترکیبات، سختی و مقاومت در برابر سایش، پلی الهای آلیفاتیک - خاصیت ارتجاعی، واحدهای ساختاری سیکلوآلیفاتیک - تعادل خصوصیات را ایجاد می کنند.
محلول های رزین آلکیدی با پارامترهای زیر مشخص می شوند:
- ویسکوزیته - 35-100 ثانیه (طبق ویسکومتر VZ-4)؛
- وزن مولکولی - 1500-5000 کیلو دالتون؛
- دانسیته - 0.9-1.05 g/cm3;
- میزان هیدروکسید پتاسیم که شاخص اصلی کیفیت روغن هاست بیش از 20 نیست.
با افزایش دما، ویسکوزیته آلکیدها کاهش می یابد و بالعکس. هر چه مقدار چربی یک ماده کمتر باشد، در هیدروکربن های آلیفاتیک و نفتنیک بدتر حل می شود.
بهبود خواص
آلکیدهای اصلاح نشده لایههای سخت و شکننده تشکیل میدهند و ضعیف حل میشوند. برای بهبود کیفیت آنها، اجزای اضافی به ترکیب مخلوط واکنش وارد می شود که به پوشش ها براقیت، الاستیسیته، مقاومت در برابر آب، حلال ها، روغن ها و هوازدگی می بخشد، خشک شدن را در دمای اتاق تسریع می کند و چسبندگی را با مواد پایه افزایش می دهد. رزین های آلکیدی اصلاح شده با استفاده از دانه کتان، روغن بلند، روغن تونگ، روغن آفتابگردان، روغن کرچک، روغن پنبه دانه، رزین، اسیدهای چرب مصنوعی به دست می آیند.
3 روش اصلی اصلاح وجود دارد:
- معرفی مونومرها در تولید رزین؛
- با واکنش آلکیدهای تمام شده با عوامل اصلاح کننده؛
- اختلاط رزین ها با دیگر فیلم سازها.
دریافت
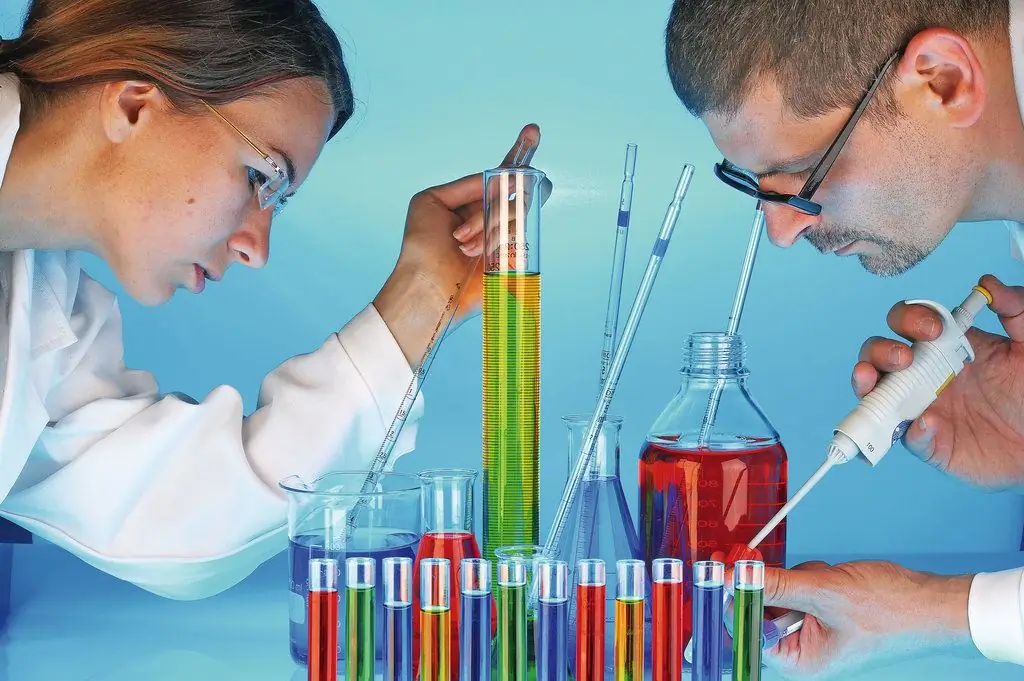
آلکیدها به دو روش سنتز می شوند: الکلیزاسیون و روش اسید چرب.
در حالت اول، فرآیند در 3 مرحله انجام می شود:
- ترانس استریفیکاسیون روغن نباتی یا تری گلیسیرید اسیدهای چرب آن با الکل های پلی هیدریک. واکنش شیمیایی در دمای 240-260 درجه سانتی گراد و در حضور کاتالیزور انجام می شود. برای تولید رزین های گلیفتالیک از الکل ها، از گلیسیرین، برای رزین های تریفتالیک - تریول، برای رزین های پنتافتالیک - پنتا اریتریتول استفاده می شود.
- استری کردن استرهای جزئی با انیدرید فتالیک که منجر به یک استر اسیدی می شود.
- پلی استریفیکاسیون با آزادسازی آب و تشکیل آلکید.
روش دوم برای تولید رزین ها، استریفیکاسیون و پلی استریفیکاسیون استرهای اسیدهای چرب و الکل های پلی هیدریک است.
رقیق کننده های آلکیدی
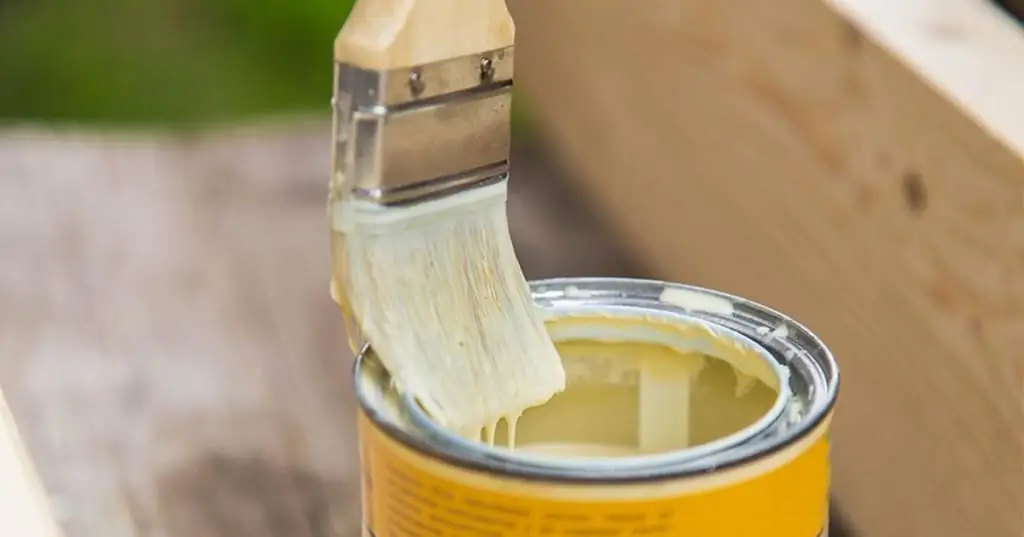
ترکیبات کربنی زیر به عنوان حلال برای رزین های آلکیدی عمل می کنند:
- آلیفاتیک (هگزان، هپتان، پارافین های C6-C12)؛
- معطر (بنزن، حلال، تولوئن، زایلن و غیره)؛
- ترپن (سقز)؛
- هالوژنه (تری کلرواتیلن، تتراکلراتیلن، پرکلرواتیلن)؛
- نفت (نفرس، بنزین).
اترهای با جوش کم (اتیل الکل، اتیل استات)، گلیکول اترها، کتون ها (استون) نیز می توانند به عنوان رقیق کننده استفاده شوند. بوتانول برای این اهداف نامناسب است، زیرا مولکول های آن مقدار زیادی از حلال موجود در رزین های آلکیدی را به خود جذب می کنند. آلکیدهای بدون چربی فقط در هیدروکربن های معطر حل می شوند، در حالی که آلکیدهای چرب در آلیفاتیک حل می شوند.
رزین های محلول در آب نیز وجود دارد که بر اساس آنها پوشش های متخلخل در آب (لعاب ها و پرایمرهای خشک شونده گرم) تولید می شود.
برنامه
هدف اصلی رزین های آلکیدی تولید رنگ و لاک الکل (LKM) است. از ترکیبات اصلاح نشده برای ساخت لاک و چسب های عایق الکتریکی استفاده می شود.
ازمحلول های رزین لاک های نیمه تمام و تمام شده را می سازند که در صنعت و زندگی روزمره استفاده می شوند.
مواد رنگ

پوشش های آلکیدی بیشترین استفاده را در بین تمام مواد بر پایه رزین های پلی تراکم دارند. از آنجایی که الکل پنتا اریتریتول دارای 4 گروه هیدروکسیل است، آلکیدهای حاوی پنتا اریتریتول سریعتر درمان می شوند و پوشش های براق تری تولید می کنند. در این راستا، صنعت عمدتاً مواد رنگ آمیزی بر پایه رزین های آلکیدی از نوع پنتافتالیک تولید می کند. استفاده از تعداد زیادی از اجزای معطر، سختی و مقاومت پوشش ها را در برابر تنش های مکانیکی تضمین می کند.
پوشش های رنگدانه ای مبتنی بر آلکیدها به گروه های زیر تقسیم می شوند:
- گلیفتالیک (GF)، پنتافتالیک (EF)، تریفتالیک (ET) لعاب؛
- خاک؛
- بتونه.
رزینهای آلکیدی خشککننده بهعنوان فیلمساز مستقل برای رنگها و لاکها، و غیرخشککنندهها در فرمولاسیون با رزینهای کاربامید، نیتراتهای سلولز (برای بهبود خاصیت ارتجاعی و چسبندگی پوششها به مواد پایه) استفاده میشوند.
خواص پوشش ها به ترکیب شیمیایی آنها بستگی دارد. بنابراین، رزینهای آلکیدی چربتر در حلالهای آلی به راحتی با برس اعمال میشوند، خاصیت ارتجاعی و مقاومت در برابر آب و هوا را افزایش میدهند، اما کندتر خشک میشوند و در برابر روغنهای معدنی مقاومت کمتری دارند. حداکثر سرعت خشک شدن برای رزین های اصلاح شده با تونگ یا بذر کتان معمول است.روغن متوسط زمان خشک شدن میناهای آلکیدی 24 ساعت است.
رنگآمیزی خاص
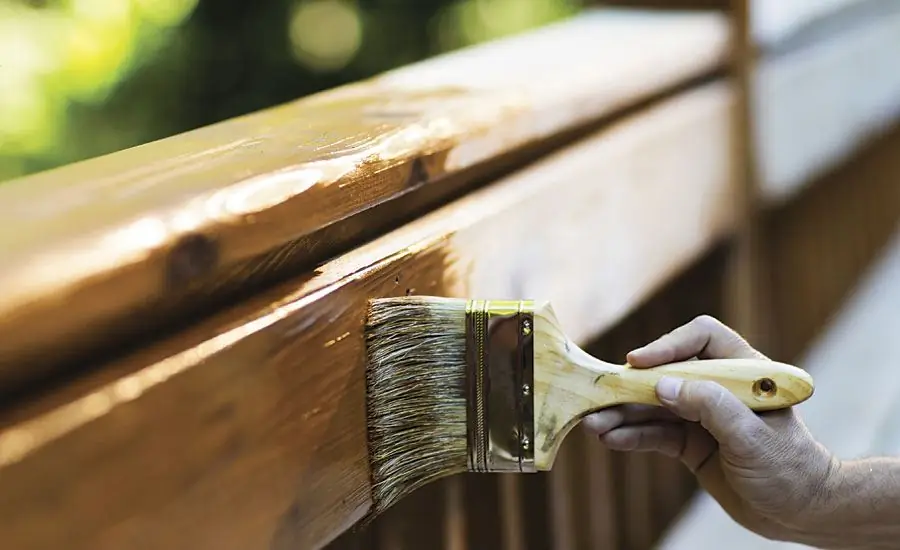
رزین های آلکیدی، بسته به ترکیب اجزا، برای اهداف زیر استفاده می شود:
- بر اساس اسید بنزوئیک (میزان روغن 38-50٪ وزنی) - لعاب برای رنگ آمیزی ماشین آلات کشاورزی، رادیاتور، تعمیرات ماشین. بسیار مقاوم در برابر محو شدن و آب و هوا.
- حاوی اسیدهای 9،12-لینولئیک و 9،11-لینولئیک - تعمیر تجهیزات.
- لاغر - خشک شدن سریع تک لایه، پرایمر، رنگ رادیاتور.
- روی روغن بذر کتان و گلیسیرین - پوشش های ضد خوردگی، جوهرهای چاپ. هنگامی که در معرض نور خورشید قرار می گیرند می توانند به سرعت محو شوند، بنابراین اغلب در پرایمرها و ترکیبات تراز کننده استفاده می شوند.
- روکش های رویی بر پایه سویا یا روغن بلند با مقاومت خوب در برابر آب و هوا.
- اصلاح شده با رزین های طبیعی (اسیدهای روزین) - تولید پرایمرها و پرکننده ها. ترکیبات مستعد محو شدن هستند.
- اصلاح شده با استایرن، آکریلات - پرایمرها، بتونهها، ترکیبات تسطیح، پوششهای رنگآمیزی کشتیها، تجهیزات، ورقهای فلزی، چوب تحت فشار مکانیکی قوی (لاکهای پارکت، لعابهای کف، مبلمان). بسته بندی لعاب در لوله آنها مقاومت بیشتری در برابر سایش و کشسانی دارند.
جنبه های زیست محیطی
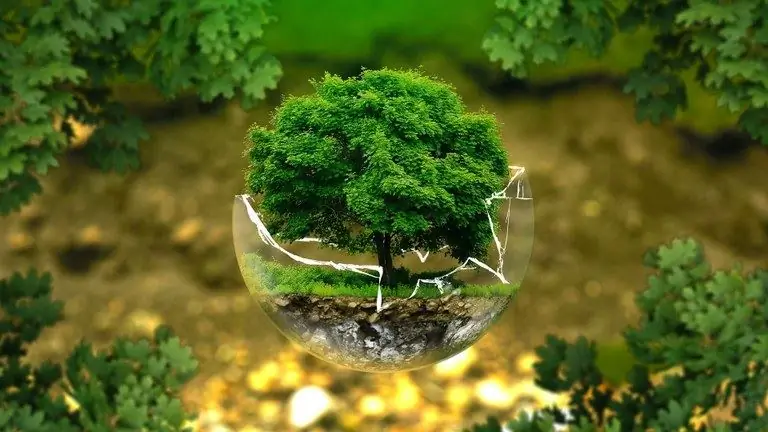
از آنجایی که رزین های آلکیدی حاوی حلال های آلی هستند، خطر خاصی برای سلامت انسان و محیط زیست دارند. هنگام انجام کار رنگ و لاک با استفاده از مواد رنگ آمیزی بر اساس آنها، لازم است از تجهیزات محافظ شخصی (ماسک گاز، روپوش) استفاده شود. رنگآمیزی باید در اتاقهایی انجام شود که دارای تهویه هوا و اگزوز هستند.
با توجه به سطح سمیت حلال ها، آلکیدها را می توان به 3 گروه تقسیم کرد:
- کمترین سمیت (MPC=300-1000 mg/m3) - اتیل اتر، الکل، بنزین؛
- سمیت متوسط (MPC=100-200 mg/m3) - استون، بوتیل اتر؛
- خیلی سمی (MPC=20-50 mg/m3) - اتیلن گلیکول، بنزن.
در خارج از کشور، الزامات زیادی برای سازگاری با محیط زیست برای تولید پوشش ها وجود دارد، بنابراین، در حال حاضر کار برای ایجاد موادی با محتوای بالای ماده خشک و ترکیبات موجود در آب در حال انجام است. با این حال، رزینهای آلکیدی با حلالهای آلی هنوز از نظر خواص پردازش بهتر از رزینهای محلول در آب عمل میکنند.